Industrial chillers play a crucial role in many industries. They provide the necessary cooling to keep processes running smoothly and efficiently.
Understanding how these complex machines work can be a daunting task. But it’s essential for those involved in their operation and maintenance.
In this article, we’ll delve into the inner workings of an industrial chiller. We’ll explore the principles behind its operation, the components involved, and its role in industrial cooling systems.
This guide will help you understand the basics of industrial chiller operations. Useful for engineers, facility managers, and anyone interested in learning more.
We’ll also touch on the importance of energy efficiency and regular maintenance in ensuring optimal performance.
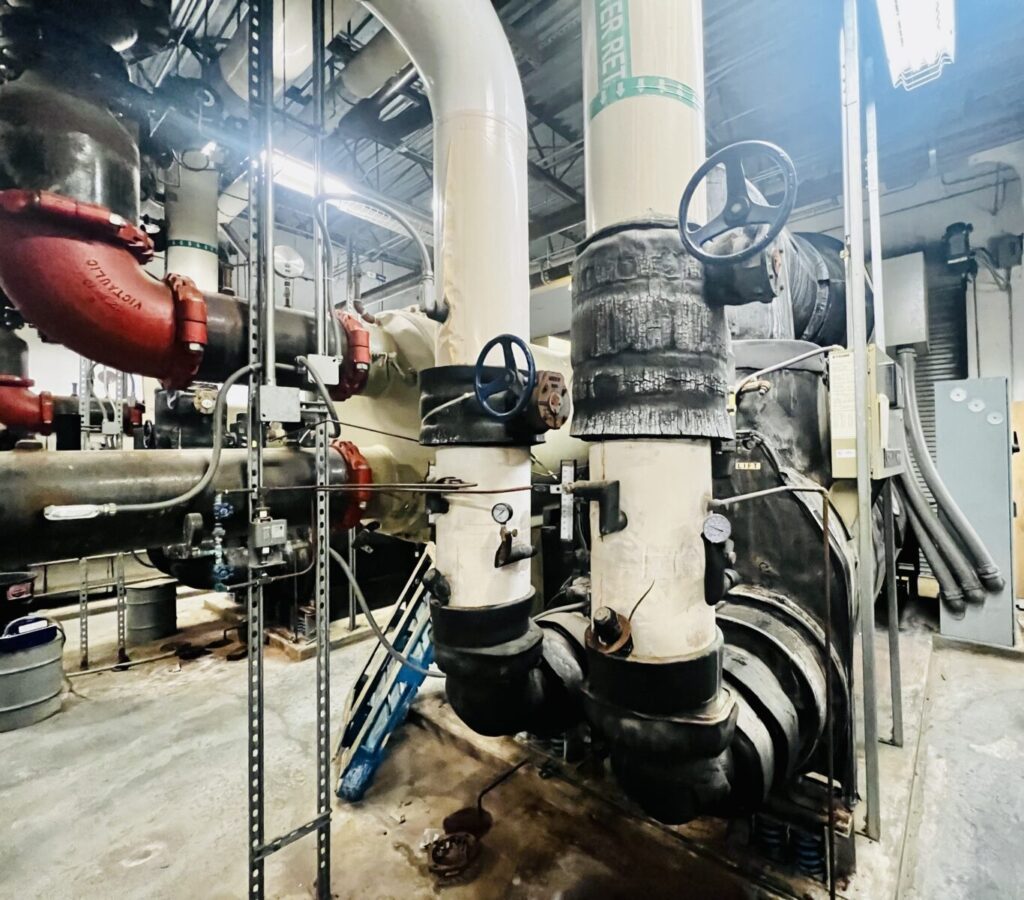
Understanding Industrial Chillers
Industrial chillers are refrigeration units designed to cool fluids or dehumidify air in industrial applications. They are integral to many processes, from manufacturing to HVAC systems in large buildings.
The process consists of four main steps: vaporization, pressurization, cooling, and enlargement. An industrial chiller removes heat from a process or space and releases it outside.
The chiller removes heat and releases it into the ambient air. This helps to cool down the process or area. This cooling is achieved through a refrigeration cycle, which we’ll explore in the next section.
The Refrigeration Cycle Explained
The refrigeration cycle is the heart of the industrial chiller operation. It involves four main stages: evaporation, compression, condensation, and expansion.
- Evaporation: The refrigerant absorbs heat from the process fluid and evaporates.
- Compression: The refrigerant vapor is compressed, raising its pressure and temperature.
- Condensation: The high-pressure refrigerant releases its heat into the environment and condenses back into a liquid.
- Expansion: The high-pressure liquid refrigerant is expanded, reducing its pressure and temperature, ready to absorb heat again.
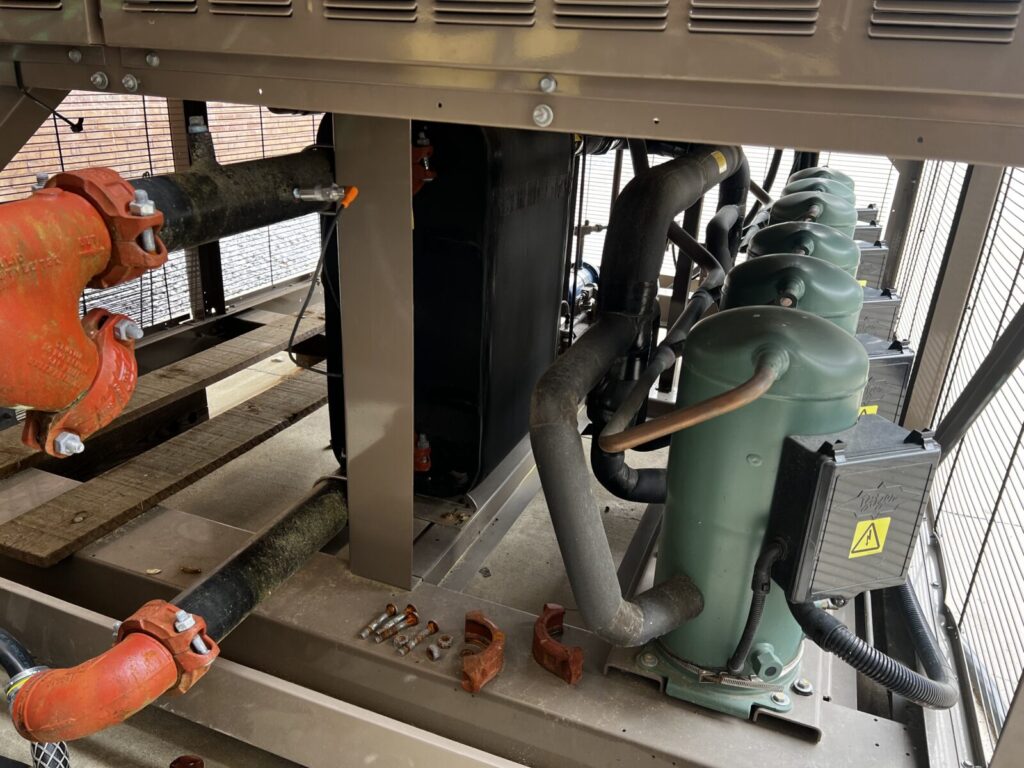
Evaporator: The Heat Absorber
The evaporator is where the refrigeration cycle begins. It’s a heat exchanger that allows the refrigerant to absorb heat from the process fluid.
As the refrigerant absorbs this heat, it changes from a low-pressure liquid into a low-pressure gas. This process is known as evaporation.
Compressor: The Pressure Raiser
The compressor is the next stage in the cycle. It takes the low-pressure refrigerant gas from the evaporator and compresses it.
This compression raises both the pressure and temperature of the refrigerant, preparing it for the next stage.
Condenser: The Heat Dissipater
The condenser is another heat exchanger, but it works oppositely to the evaporator. It allows the refrigerant to release the heat it absorbed earlier.
As the refrigerant releases this high-temperature heat, it changes back into a high-pressure liquid. This process is known as condensation.
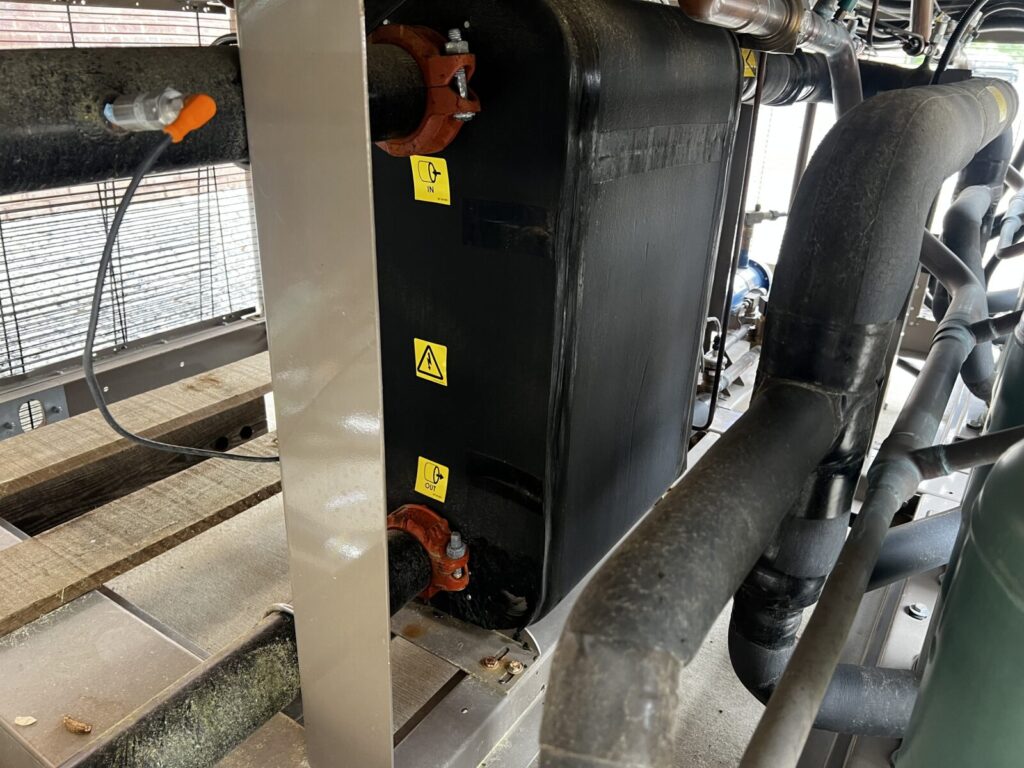
Expansion Valve: The Pressure Reducer
The final stage of the refrigeration cycle involves the expansion valve. This device reduces the pressure of the high-pressure liquid refrigerant from the condenser.
As the refrigerant’s pressure drops, so does its temperature, making it ready to absorb more heat in the evaporator.
Key Components of an Industrial Chiller
An industrial chiller is made up of several key components. These include the evaporator, compressor, condenser, and expansion valve, which we’ve already discussed.
In addition to these, there’s the refrigerant. This is the substance that circulates through the chiller, absorbing and releasing heat as it goes.
The Role of Refrigerants
Refrigerants play a crucial role in the operation of an industrial chiller. They are the medium that carries heat from one place to another.
Different types of refrigerants are used in chillers, each with its own properties. The choice of refrigerant can affect the chiller’s efficiency, environmental impact, and safety.
Types of Industrial Chillers
Industrial chillers come in various types, each designed for specific cooling solutions applications and environments. The most common types are air-cooled and water-chillers with cooling towers.
- Air-cooled chillers use air to remove heat from the refrigerant.
- Water-cooled chillers use water for the same purpose.
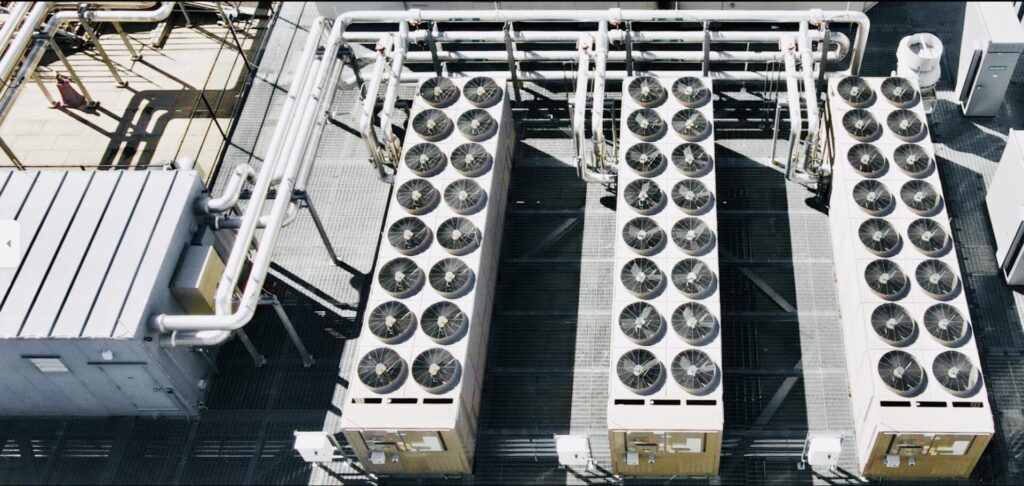
Air-Cooled vs. Water-Cooled Chillers
Air-cooled and water-cooled chillers are the most commonly used types in industrial settings. Each has its own advantages and considerations.
Air-cooled chillers are generally simpler and less expensive to install. They don’t require a cooling tower, which saves space and reduces maintenance. However, they are less efficient than water-cooled chillers, especially in hot climates.
Water-cooled chillers, on the other hand, are more efficient and can handle larger cooling loads. They are ideal for situations where high performance is a priority.
They need a cooling tower to cool down the warm condenser water. They also need access to a water source. This may lead to higher installation and maintenance expenses.
Energy Efficiency and Industrial Chillers
Energy efficiency is a crucial factor in industrial chiller operations. A highly efficient chiller can significantly reduce energy consumption, leading to lower operational costs.
It’s important to consider factors such as the chiller’s Coefficient of Performance (COP), part-load efficiency, and the use of variable speed drives. These can greatly influence the chiller’s overall energy efficiency. Regular maintenance and proper sizing are also key to ensuring optimal efficiency.
Maintenance and Troubleshooting
Regular maintenance is vital for the smooth operation of industrial chillers. It helps prevent unexpected breakdowns, prolongs the chiller’s lifespan, and maintains its efficiency.
Common maintenance tasks include:
- Regular inspection of all components
- Cleaning of the condenser and evaporator tubes
- Checking and refilling refrigerant levels
- Lubricating moving parts
- Checking and adjusting controls and safety devices
Troubleshooting is another important aspect. Common issues include refrigerant leaks, compressor failures, and poor heat transfer. Understanding the operation of the chiller and its components can help in identifying and resolving these issues promptly.
Conclusion
Understanding the operation of industrial chillers is crucial for their efficient use. It helps in troubleshooting, maintenance, and making informed decisions about their installation and use.
In conclusion, industrial chillers play a vital role in various industries. Their operation involves complex processes and components, but with the right knowledge, their benefits can be fully harnessed.
Leave a Reply